Thanks ErickC for the
tip with the physics files. So I added these variables to the wagon's wag file:
ORTSLengthBogieCentre ( 14 )
ORTSLengthCarBody ( 19.2 )
ORTSLengthCouplerFace ( 20,478 )
ORTSNumberAxles ( 6 )
ORTSNumberBogies ( 2 )
But unfortunately there was no change in the behavior of the wagon's bogies in the curve.
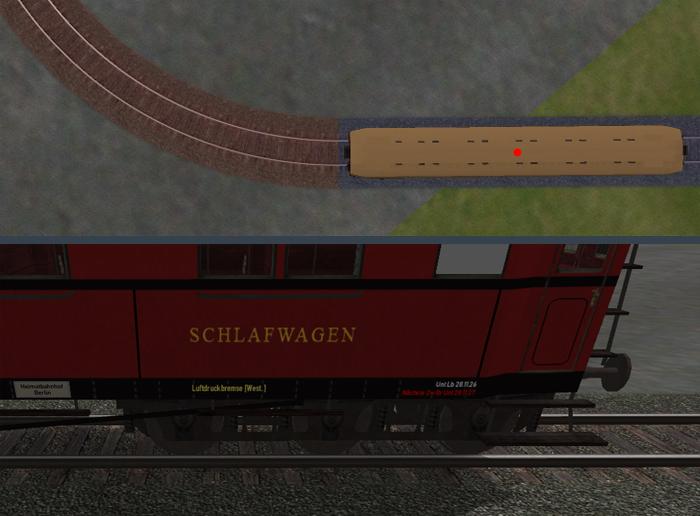
Everything is ok on the straight track.
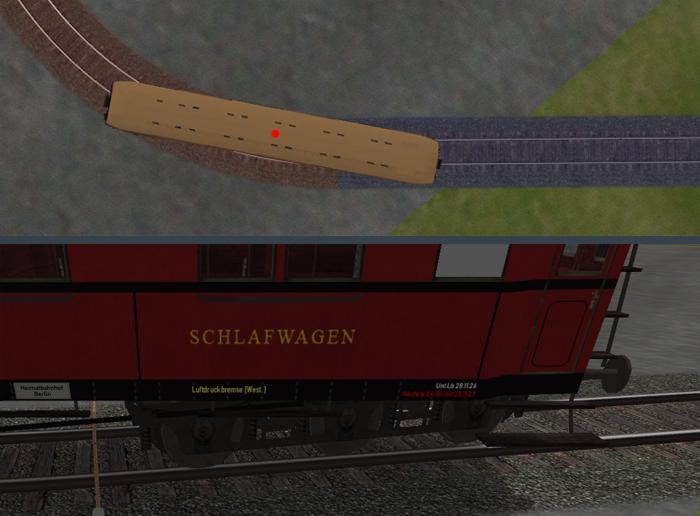
One bogie is still on the straight track, but the car body has already entered the curve.
Of course, a rotation of the bogie relative to the car body is already correct here. But the bogie is "twisted" more than necessary.
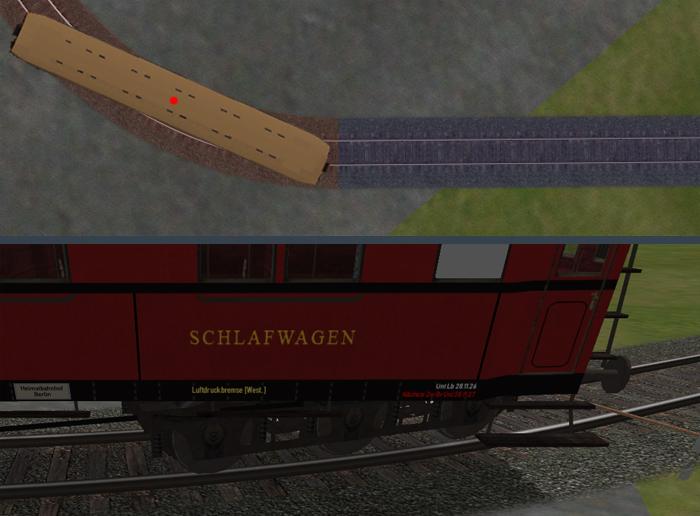
The entire wagon is on the curve.
Thanks Laci1959 for the
tip that OR generally assumes 4 axles per bogie. At least that explains the specific bogie “twist”.
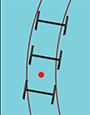
The pivot point of the bogie is actually calculated by OR between the second and third axles. So it is somewhere else as I set it in the model.
The rotation of a bogie is probably calculated in OR using the position of the car body pivot (red dot in the images) in the curve. So the specific position of the bogie pivot over the track vector is not taken into account, but only the car body pivot. Based on this, the rotation of the bogies is then calculated, depending on the position of the curve. In my opinion, there would be nothing wrong with that if the specific dimensions of the car body and bogies were taken into account. Unfortunately, specifying the dimensions, as mentioned above, did not help.
I have to admit without envy that MSTS works much better here. Apparently MSTS determines the pivots of the bogies defined in the model shape and then takes these into account with their respective positions over the track vectors.
As a car modeler, I am of course interested in this topic, but on the other hand I have to admit that I rarely pay attention to the exact curves of the bogies in the game. In addition, I tried it here for the screenshots with an extreme curve, the narrowest radius of the dynamic track. It is doubtful whether the bogie "over-rotation" would still be perceived as annoying even in gentle, wide curves with a larger radius.
Incidentally, I found the variables used above, such as ORTSNumberAxles, in the OR manual only under Derailment Coefficient, so they otherwise seem to have no intended effect on the adaption to the curve, but primarily play a role in derailment.
Coming back to the actual topic here, the programming implementation of laterally movable axles in curves seems to me to be quite ambitious - at least as long as it works as analyzed above. So an MSTS-like exact calculation of the exact bogie positions above the track would actually have to be carried out before one should then think about laterally movable axles - probably a more extensive programming construction site.
What I often observe when driving over switch roads is a short, tremble turning of bogies in general. Maybe this also has something to do with the bogie calculation using the car body center. So it's good that this topic was addressed here I think.