Braking - Wheel Skid
#1
Posted 20 April 2016 - 07:14 PM
During a braking operation if the wheel rotation is restricted sufficiently by the brake shoes (brake force) then it is possible for the wagon wheel to lose its 'grip' and skid on the rails. When a skid is induced the rails can be damaged, and the train can become a lot harder to manage and stop.
Is there an interest in this feature being added to OR?
If introduced it would only be a basic model first, and may not take into account any anti-skid devices on newer stock.
It may also uncover poorly defined wagon files with large values of MaxBrakeForce.
#2
Posted 20 April 2016 - 07:38 PM
steamer_ctn, on 20 April 2016 - 07:14 PM, said:
It is always worthwhile to read what you're interested in, Peter. I really cannot comment on your idea - just don't know enough (yet).
But, I do have a question. In another thread, - that I cannot locate - there was a mention of the MaxBrakeForce value in wagons being too high in many cases.
What would be a range of values (ballpark figures / high to low ) that would work for wag files?
#3
Posted 20 April 2016 - 07:58 PM
steamer_ctn, on 20 April 2016 - 07:14 PM, said:
During a braking operation if the wheel rotation is restricted sufficiently by the brake shoes (brake force) then it is possible for the wagon wheel to lose its 'grip' and skid on the rails. When a skid is induced the rails can be damaged, and the train can become a lot harder to manage and stop.
Is there an interest in this feature being added to OR?
If introduced it would only be a basic model first, and may not take into account any anti-skid devices on newer stock.
It may also uncover poorly defined wagon files with large values of MaxBrakeForce.
YES
To do a complete feature set will will require more than just skidding the wheels tho. AFAIK from reading mechanical drawings of the brake system as well as steam era literature MaxBreakForce() needs to be set in the range of 0.6 to 0.7 of the value of Mass() for the empty car. There are going to be a whole lot of .wags where that isn't the case and so adding the feature will probably require additio0n of an option to turn the feature off or on.
There is also the question of the empty/load brake, something that's pretty standard since the 1930's for cars that have a significant difference in Mass() when comparing the empty car to a loaded car -- cars like hoppers carrying coal or iron ore. The apparatus was simple: a lever positioned near the side sill at the trucks that would increase the brake force when the distance between the sill and truck frame was reduced (on account of a heavy lading) and return it to normal when the distance grew again after discharging the lading.
And so there will be a need to expand the parameter list for these cars to include a second "MaxBrakeForce()" as well as some value of Mass() to determine which of those two should be used.
It's not complex... just a bit more work to do it all.
FWIW skids produce a flat spot on wheels... they go whack whack WHACK! with every rotation.
#4
Posted 21 April 2016 - 02:47 AM
I'll just go and get my medication........
#5
Posted 21 April 2016 - 03:19 AM
R H Steele, on 20 April 2016 - 07:38 PM, said:
Have a look at this calculator, as I built it based upon some of the suggested values from Westinghouse.
Genma Saotome, on 20 April 2016 - 07:58 PM, said:
I will create a blue print for it, and start working on it. (Update date - TBA)
Genma Saotome, on 20 April 2016 - 07:58 PM, said:
I have seen the following brake ratio figures quoted, and they are used in the calculator in the link above.
goods_br=0.68; // Brake ratio for goods
pass_br=0.82; // Brake ratio for pass
hand_br=0.2; // Brake ratio for handbrake
tender_br=0.82; // Brake ratio for tender
loco_br=0.75; // Brake ratio for locomotive
EDIT: I was contemplating linking it to the advanced adhesion model option. I am reluctant to add another "on/off" option as I think we have too many now as it is. This is probably another full thread worth of discussion.
Genma Saotome, on 20 April 2016 - 07:58 PM, said:
And so there will be a need to expand the parameter list for these cars to include a second "MaxBrakeForce()" as well as some value of Mass() to determine which of those two should be used.
I agree that the variable mass of a vehicle needs to be looked at. Carlo and I have had some discussions about addressing it.
keystoneaholic, on 21 April 2016 - 02:47 AM, said:
Interesting idea, but I think that the trees would have to be in close proximity to the tracks to be realistic. Having friction change if a tree is say 100m away from the track might be a bit of a stretch.
I have seen friction figures of down around 0.1 (10%) for leaves on the track, so it could be quite a slippery effect.
#6
Posted 21 April 2016 - 03:40 AM
Will you program friction between the brake shoe and wheels? And between brake linings and brake disc?
#7
Posted 21 April 2016 - 04:51 AM
Oh and how about new track dynamics to account for the broken rail caused by severe flat spots.
The possibilities are endless. :lol2:
Steve
#8
Posted 21 April 2016 - 06:23 AM
Steve has stated that we all know and are aware of the many, many variants , but just keep it as simple as possible , yet functional without too many frills . It'll work just fine .
Just an opinion .
#9
Posted 21 April 2016 - 07:49 AM
WRT values, all of the brake system mechanical drawings I have (many) from the New York Central (a very large American road) all say the same thing for boxcars and gondolas: 60% of empty weight. OTOH identical drawings from other railroads cite 70%. My hunch is everybody knew there was an ideal range of 60-70% and picked a number that "felt right" as it was impossible to know for sure. Given that the laws of physics are true everywhere it stands to reason that said guideline should apply to all freight cars.
WRT locomotives... I've seen the same value you cite.
#10
Posted 21 April 2016 - 10:58 AM
hroch, on 21 April 2016 - 03:40 AM, said:
Will you program friction between the brake shoe and wheels? And between brake linings and brake disc?
Cast-iron tread brakes are speed dependant with the same brake force. The lower the speed, the more risk of wheel slide.
keystoneaholic, on 21 April 2016 - 02:47 AM, said:
I agree. Also this autumn theme was mention for MSTS but was never implemented.
Thanks
#11
Posted 21 April 2016 - 11:26 AM
Good start would add the advance adhesion to WAG an not just ENG braking. But you also if it would be possible is have a optional wag/eng parameter to have flat spot rates for first game loads present since some switching activities have it where you move bad order cars. Changes in force depending on a stocks wheel roundness we also need changes in vibration as well as osculating friction forces after severe sliding. Momentum for car to increase flat spot inches is by the amount of time, weight an feet a WAG/ENG is dragged sliding. Heavy braking force I indeed a number of times have seen empty cars slide especially with hand brakes applied but with loaded heavy cars I have seen them rarely slide during heavy braking an with hand brakes as its just like light locomotives with high brake forces slide while heavy ones with same amount of force continue to roll.
Severe flat spots more then 2 inches at high speeds can cause cars to overturn or during shoves or pushes cause a jackknife especially during heavy power braking.
#12
Posted 21 April 2016 - 01:45 PM
hroch, on 21 April 2016 - 03:40 AM, said:
The MaxBrakePower figure in the WAG file represents the force applied to the wheel by the brake, and should have an appropriate allowance for the relevant friction values.
The braking forces are quite complex, and the friction will vary with the brake cylinder pressure, the speed of the train, type of brake shoe, etc. As has been suggested elsewhere in the thread, the model will be a simple adaptation which hopefully will provide a balance between complexity and a reasonable representation of the prototypical behavior.
For example, currently OR appears to apply a constant brake force regardless of the speed of the train. Based upon some figures that I have seen in my research, the friction coefficient for cast iron brake shoes @ 0mph is 0.33, whilst the value at 60mph is 0.074. This means that the brake force @ 60mph will only be 20% of the lower speed value (and the value currently applied by OR).
So I am interested in incorporating a change of friction with speed factor into OR, as I suspect this will have a impact on the performance of the train compared to its current behavior. Using the above forces example, trains operating at high speeds will take longer to stop at the same brake applications as used now, or alternatively higher brake application rates will be required.
ATW, on 21 April 2016 - 11:26 AM, said:
My understanding of the code at the moment is that the advanced adhesion model does not produce wheel skids for braking, even on locomotives. Thus I don't believe that braking has been implemented into the advanced adhesion model.
Can anybody share a scenario where they have been able to get a locomotive produce a wheel skid due to braking?
#13
Posted 21 April 2016 - 02:15 PM
steamer_ctn, on 21 April 2016 - 01:45 PM, said:
Are you planning this for all types of traction? I have already started a thread for this very purpose!
steamer_ctn, on 21 April 2016 - 01:45 PM, said:
My understanding of the code at the moment is that the advanced adhesion model does not produce wheel skids for braking, even on locomotives. Thus I don't believe that braking has been implemented into the advanced adhesion model.
Can anybody share a scenario where they have been able to get a locomotive produce a wheel skid due to braking?
I always use advanced adhesion but i have not yet use the ORTS Adhesion parameter. The only way i can get wheel slide atm is to set the wheel radius smaller or use a very low adhesion value in the experimental tab section.
The wheels on the model actually do lock as well, along with the speedometer reading zero!
Thanks
#14
Posted 21 April 2016 - 02:41 PM
steamer_ctn, on 21 April 2016 - 01:45 PM, said:
My understanding of the code at the moment is that the advanced adhesion model does not produce wheel skids for braking, even on locomotives. Thus I don't believe that braking has been implemented into the advanced adhesion model.
Can anybody share a scenario where they have been able to get a locomotive produce a wheel skid due to braking?
I got it a number of times during heavy dynamic braking as well as independent braking. Use both Loco braking an Dynamic braking at same time which is forbidden by real rail rules I have got wheels to slide where my engines are moving still to a stop but my cab Speedometer is at 0MPH because my wheels were sliding.
Try testing it with a light mass unit with high braking forces or even try it with a unit moving an applying the locomotives handbrake if equipped.
#15
Posted 22 April 2016 - 01:50 AM
steamer_ctn, on 21 April 2016 - 01:45 PM, said:
Yes you are right. But for disc brakes coefficient friction between brake linings and brake disc is higher.
For example:
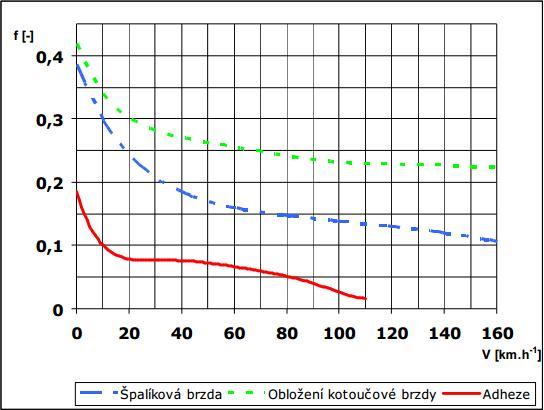
green curve for disc brakes
blue curve for shoe brake
red curve for adhesion
Would it be possible to program the two curves? One for shoe brake and other for dics brake.