Braking - Wheel Skid
#11
Posted 21 April 2016 - 11:26 AM
Good start would add the advance adhesion to WAG an not just ENG braking. But you also if it would be possible is have a optional wag/eng parameter to have flat spot rates for first game loads present since some switching activities have it where you move bad order cars. Changes in force depending on a stocks wheel roundness we also need changes in vibration as well as osculating friction forces after severe sliding. Momentum for car to increase flat spot inches is by the amount of time, weight an feet a WAG/ENG is dragged sliding. Heavy braking force I indeed a number of times have seen empty cars slide especially with hand brakes applied but with loaded heavy cars I have seen them rarely slide during heavy braking an with hand brakes as its just like light locomotives with high brake forces slide while heavy ones with same amount of force continue to roll.
Severe flat spots more then 2 inches at high speeds can cause cars to overturn or during shoves or pushes cause a jackknife especially during heavy power braking.
#12
Posted 21 April 2016 - 01:45 PM
hroch, on 21 April 2016 - 03:40 AM, said:
The MaxBrakePower figure in the WAG file represents the force applied to the wheel by the brake, and should have an appropriate allowance for the relevant friction values.
The braking forces are quite complex, and the friction will vary with the brake cylinder pressure, the speed of the train, type of brake shoe, etc. As has been suggested elsewhere in the thread, the model will be a simple adaptation which hopefully will provide a balance between complexity and a reasonable representation of the prototypical behavior.
For example, currently OR appears to apply a constant brake force regardless of the speed of the train. Based upon some figures that I have seen in my research, the friction coefficient for cast iron brake shoes @ 0mph is 0.33, whilst the value at 60mph is 0.074. This means that the brake force @ 60mph will only be 20% of the lower speed value (and the value currently applied by OR).
So I am interested in incorporating a change of friction with speed factor into OR, as I suspect this will have a impact on the performance of the train compared to its current behavior. Using the above forces example, trains operating at high speeds will take longer to stop at the same brake applications as used now, or alternatively higher brake application rates will be required.
ATW, on 21 April 2016 - 11:26 AM, said:
My understanding of the code at the moment is that the advanced adhesion model does not produce wheel skids for braking, even on locomotives. Thus I don't believe that braking has been implemented into the advanced adhesion model.
Can anybody share a scenario where they have been able to get a locomotive produce a wheel skid due to braking?
#13
Posted 21 April 2016 - 02:15 PM
steamer_ctn, on 21 April 2016 - 01:45 PM, said:
Are you planning this for all types of traction? I have already started a thread for this very purpose!
steamer_ctn, on 21 April 2016 - 01:45 PM, said:
My understanding of the code at the moment is that the advanced adhesion model does not produce wheel skids for braking, even on locomotives. Thus I don't believe that braking has been implemented into the advanced adhesion model.
Can anybody share a scenario where they have been able to get a locomotive produce a wheel skid due to braking?
I always use advanced adhesion but i have not yet use the ORTS Adhesion parameter. The only way i can get wheel slide atm is to set the wheel radius smaller or use a very low adhesion value in the experimental tab section.
The wheels on the model actually do lock as well, along with the speedometer reading zero!
Thanks
#14
Posted 21 April 2016 - 02:41 PM
steamer_ctn, on 21 April 2016 - 01:45 PM, said:
My understanding of the code at the moment is that the advanced adhesion model does not produce wheel skids for braking, even on locomotives. Thus I don't believe that braking has been implemented into the advanced adhesion model.
Can anybody share a scenario where they have been able to get a locomotive produce a wheel skid due to braking?
I got it a number of times during heavy dynamic braking as well as independent braking. Use both Loco braking an Dynamic braking at same time which is forbidden by real rail rules I have got wheels to slide where my engines are moving still to a stop but my cab Speedometer is at 0MPH because my wheels were sliding.
Try testing it with a light mass unit with high braking forces or even try it with a unit moving an applying the locomotives handbrake if equipped.
#15
Posted 22 April 2016 - 01:50 AM
steamer_ctn, on 21 April 2016 - 01:45 PM, said:
Yes you are right. But for disc brakes coefficient friction between brake linings and brake disc is higher.
For example:
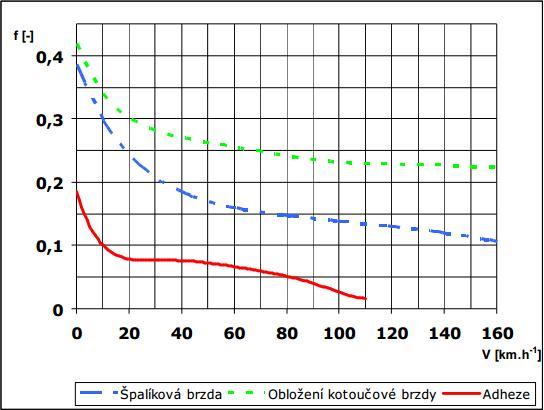
green curve for disc brakes
blue curve for shoe brake
red curve for adhesion
Would it be possible to program the two curves? One for shoe brake and other for dics brake.
#16
Posted 22 April 2016 - 02:25 AM
hroch, on 22 April 2016 - 01:50 AM, said:
Would it be possible to program the two curves? One for shoe brake and other for dics brake.
Do you have the formula for the curves?
Also a link to the reference source?
Thanks
#17
Posted 22 April 2016 - 04:39 AM
http://www.agir.ro/buletine/780.pdf
It describes coefficients of slide friction for different materials and their values correspond more or less with curves on my picture.
#18
Posted 22 April 2016 - 05:08 AM
I have a book on the engineering and design of railway brake systems. I will have a look through it as I seem to remember there is at least one graph showing the difference between cast iron shoes and Hi friction brakes.
#19
Posted 22 April 2016 - 03:19 PM
hroch, on 22 April 2016 - 04:39 AM, said:
http://www.agir.ro/buletine/780.pdf
It describes coefficients of slide friction for different materials and their values correspond more or less with curves on my picture.
copperpen, on 22 April 2016 - 05:08 AM, said:
Thanks for that I have access to this reference, and already have graphs showing the difference. I was hoping for a formula as that is easier to code.
Leave it with me.
Thanks anyway.
#20
Posted 23 April 2016 - 12:14 AM